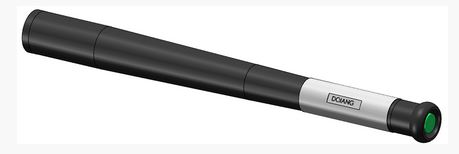
Smart Manufacturing (flashlight) Automated Production Line Training System
Courses Involved
- The principle and application of the sensor
- Production Automation and Manufacturing Systems
- Electrical Control and PLC
- Electromechanical Transmission and Control
- Computer Aided Design and Manufacturing
- Computer Control System
- Inverter Technology and Application
- Industrial Fieldbus
- Process Control
- Industrial Configuration Software Technology
- Industrial Robot
- CNC machining
- Mechanical Design Basics
- Hydraulic and pneumatic
Course coverage
- 4.1 Robotic operation: hardware connection of the robot (body, control cabinet, teach pendant, etc.);
- 4.2 Robot teaching board debugging and computer debugging;
- 4.3 Robot I/O communication (defining digital input and output signals); I/O signal monitoring and operation; robot program creation and programming; robot Ethernet communication function;
- 4.4 CNC machining: CNC system debugging; machining process design; programming process;
- 4.5 Visual guidance: communication settings between visual inspection and PLC; supporting visual software debugging;
- 4.6 Radio frequency identification: RFID and PLC communication settings; RFID wiring, signal acquisition;
- 4.7 Programming control: drawing of electrical schematic diagram ,program flow chart; programming and debugging of programmable controller; application of programming software;
- 4.8 Communication control: Ethernet communication control; network system configuration and topology layout; PLC total/slave setting; communication between PLC and RFID and robot; variable communication between PLC and man-machine interface;
- 4.9 Motor drive: servo motor positioning speed control; frequency control of three-phase gear motor;
- 4.10 Sensing detection: installation, wiring, signal acquisition and debugging of photoelectric sensors, inductors, capacitors, Hall and other switching sensors
- 4.11 Mechanical assembly: application of assembly tools, measuring tools, mechanical accessories; installation and commissioning of linear actuators, timing belt pulleys, mechanical axes with support optical axes, fixtures, etc.
- 4.12 air path construction: the drawing of the air path diagram, the construction of the air path and the installation and debugging of the pneumatic actuators, such as the blocking cylinder, the three-axis cylinder and the wide air gripper;
- 4.13 Low-voltage power distribution: wiring and debugging of buttons, indicator lights, circuit breakers, relays, tower lights, etc.
- 4.14 Human-computer interaction: interface drawing and variable debugging of man-machine configuration, application of configuration software;
- 4.15 Understand the diagram and wiring: wiring tools, wiring accessories, wire number identification; signal wire, power line wire docking.
Technical parameters
Scope of Learning
- Design and application of FANUC numerical control system (machining center, CNC lathe, CNC machining center)
- Robot application research
- Network communication technology and bus technology
- Configuration monitoring and human-machine interface technology
- Servo control technology
- Design and application of Siemens PLC
- Sensor technology and application
- Pneumatic control technology
- Motion Control System
- Mechanical structure training technology
- Fault detection technical skills training